RAPID PROTOTYPING SERVICE
Direct Metal Laser Sintering (DMLS/DMLM)
Surface Finishes & Tolerances
Typical Held Tolerance
Dimensional Accuracy
Material |
Standard |
Metric |
Aluminum (AlSi10Mg) |
±0.004inch |
±0.102mm |
Titanium (Ti64) |
±0.001inch |
±0.0254mm |
Stainless (PH1) |
±0.001inch |
±0.0254mm |
Maraging Steel (MS1) |
±0.002inch |
±0.0508mm |
Inconel (IN718) |
±0.002inch |
±0.0508mm |
Minimum Recommended Wall Thickness
Material |
Standard |
Metric |
Aluminum (AlSi10Mg) |
0.012 - 0.016 inch |
0.308-0.406mm |
Titanium (Ti64) |
0.012 - 0.016 inch |
0.308-.406mm |
Stainless (PH1) |
0.012 - 0.016 inch |
0.308-0.406mm |
Maraging Steel (MS1) |
0.008-0.020inch |
0.203-0.508mm |
Inconel (IN718) |
0.011-0.015inch |
0.279-.0381mm |
Density
All materials we use have an approximately 100% relative density
Material |
Standard |
Metric |
Aluminum (AlSi10Mg) |
0.096 lb/in3 |
2.67 g/cm3 |
Titanium (Ti64) |
0.159 lb/in3 |
4.41 g/cm3 |
Stainless (PH1) |
0.28 lb/in3 |
7.8 g/cm3 |
Maraging Steel (MS1) |
0.289 - 0.293 lb/in3 |
8.0 - 8.1 g/cm3 |
Inconel (IN718) |
0.296 lb/in3 |
8.2 g/cm3 |
Surface Finish
All surface roughness is measured in Ra (roughness average)
Material |
Surface |
Standard |
Metric |
Aluminum (AlSi10Mg) |
Horizontal |
0.00024-0.00039" |
6-10 µm |
Alum"um (AlSi10Mg) |
Vertical |
0.00118-0.00157" |
30-40 µm |
Titanium (Ti64) Performance |
Horizontal |
0.00036-0.00047" |
9-12 µm |
Titanium (Ti64) Performance |
Vertical |
0.00160-0.00320" |
40-80 µm |
Titanium (Ti64) Speed |
Horizontal |
0.00023-0.00039" |
6-10 µm |
Titanium (Ti64) Speed |
Vertical |
0.00137-0.00157" |
35-40 µm |
Stainless (PH1) |
Horizontal |
0.00010-0.00020" |
2.5-4.5 µm |
Stainless (PH1) |
Vertical |
0.00060-0.00160" |
15-40 µm |
Maraging Steel (MS1) |
Horizontal |
0.00016-0.00025" |
4-6.5 µm |
Maraging Steel (MS1) |
Vertical |
0.00078-0.00195" |
20-50 µm |
Inconel (IN718) |
Horizontal |
0.00016-0.00025" |
4-6 µm |
Inconel (IN718) |
Vertical |
0.00078-0.00195" |
20-50 µm |
Surface Finish Ra (Roughness Average)
VDI |
MICRO
METER |
MICRO
INCH |
RMS |
-2 |
0.08 |
3.14 |
3.9 |
-1 |
0.09 |
3.54 |
4.4 |
0 |
0.1 |
4 |
4.9 |
1 |
0.11 |
4.4 |
5.5 |
2 |
0.12 |
4.8 |
5.9 |
3 |
0.14 |
5.6 |
6.9 |
4 |
0.16 |
6.4 |
7.9 |
5 |
0.18 |
7.2 |
8.9 |
6 |
0.2 |
8 |
9.9 |
7 |
0.22 |
8.8 |
10.8 |
8 |
0.25 |
10 |
12.3 |
9 |
0.28 |
11.2 |
13.8 |
10 |
0.32 |
12.8 |
15.8 |
11 |
0.35 |
14 |
17.2 |
12 |
0.4 |
16 |
19.5 |
13 |
0.45 |
18 |
22 |
14 |
0.5 |
20 |
24.5 |
15 |
0.56 |
22.4 |
27 |
16 |
0.63 |
25.2 |
31.3 |
17 |
0.7 |
28 |
35.2 |
18 |
0.8 |
32 |
39 |
19 |
0.9 |
36 |
44.4 |
20 |
1 |
40 |
49.3 |
21 |
1.12 |
44.8 |
54.6 |
22 |
1.26 |
50.4 |
62.4 |
23 |
1.4 |
56 |
70.3 |
24 |
1.62 |
63 |
78 |
25 |
1.8 |
72 |
88.2 |
26 |
2 |
80 |
98.9 |
27 |
2.2 |
88 |
109.2 |
28 |
2.5 |
100 |
123.9 |
29 |
2.8 |
112 |
138.5 |
30 |
3.2 |
125 |
153.7 |
31 |
3.5 |
140.4 |
175.5 |
32 |
4 |
160 |
197.5 |
33 |
4.5 |
180 |
218.8 |
34 |
5 |
200 |
248.6 |
35 |
5.6 |
224 |
277.9 |
36 |
6.3 |
250 |
306.2 |
37 |
7 |
280 |
351 |
38 |
8 |
320 |
400 |
39 |
9 |
360 |
|
40 |
10 |
400 |
|
41 |
11.2 |
448 |
|
42 |
12.6 |
500 |
|
43 |
14 |
560 |
|
44 |
16 |
640 |
|
45 |
18 |
760 |
|
The most common surface roughness parameter is Ra, or Arithmetic It basically reflects the average height of roughness component Ra provides a simple value for accept/reject decisions. Default parameter if not otherwise specified, and available even in the least Ra is not a good discriminator for different types of surfaces as it is incapable of differentiating between "spiky" and "scratched" surfaces. |
Surface Finish Roughness Parameters
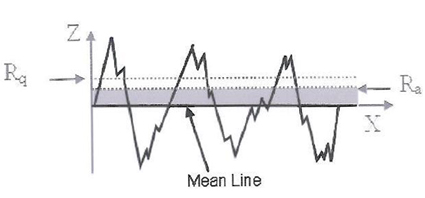 |
Surface Finish Roughness Depths
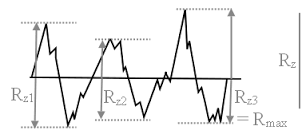 |
Surface Finish Roughness Comparison
Ra µm |
50 |
37.5 |
25 |
12.5 |
6.3 |
3.2 |
1.6 |
0.8 |
0.4 |
0.2 |
0.1 |
0.05 |
0.025 |
0.012 |
Ra µin (CLA) |
2,000 |
1,500 |
1,000 |
500 |
250 |
125 |
63 |
32 |
16 |
8 |
4 |
2 |
1 |
0.5 |
Tube Finishing |
|
|
|
|
|
|
|
|
|
|
|
|
|
|
|
|
|
|
|
|
|
|
|
|
|
|
|
|
Hot Extruded |
|
|
|
|
|
|
|
|
|
|
|
|
|
|
|
|
|
|
|
|
|
|
|
|
|
|
|
|
Cold Drawn |
|
|
|
|
|
|
|
|
|
|
|
|
|
|
|
|
|
|
|
|
|
|
|
|
|
|
|
|
Smooth Bore |
|
|
|
|
|
|
|
|
|
|
|
|
|
|
|
|
|
|
|
|
|
|
|
|
|
|
|
|
Electroplished |
|
|
|
|
|
|
|
|
|
|
|
|
|
|
|
|
|
|
|
|
|
|
|
|
|
|
|
|
Metal Cutting |
|
|
|
|
|
|
|
|
|
|
|
|
|
|
|
|
|
|
|
|
|
|
|
|
|
|
|
|
Sawing |
|
|
|
|
|
|
|
|
|
|
|
|
|
|
|
|
|
|
|
|
|
|
|
|
|
|
|
|
Planing,Shaping |
|
|
|
|
|
|
|
|
|
|
|
|
|
|
|
|
|
|
|
|
|
|
|
|
|
|
|
|
Drilling |
|
|
|
|
|
|
|
|
|
|
|
|
|
|
|
|
|
|
|
|
|
|
|
|
|
|
|
|
Milling |
|
|
|
|
|
|
|
|
|
|
|
|
|
|
|
|
|
|
|
|
|
|
|
|
|
|
|
|
Boring, Turning |
|
|
|
|
|
|
|
|
|
|
|
|
|
|
|
|
|
|
|
|
|
|
|
|
|
|
|
|
Broaching |
|
|
|
|
|
|
|
|
|
|
|
|
|
|
|
|
|
|
|
|
|
|
|
|
|
|
|
|
Reaming |
|
|
|
|
|
|
|
|
|
|
|
|
|
|
|
|
|
|
|
|
|
|
|
|
|
|
|
|
Abrasive |
|
|
|
|
|
|
|
|
|
|
|
|
|
|
|
|
|
|
|
|
|
|
|
|
|
|
|
|
Grinding |
|
|
|
|
|
|
|
|
|
|
|
|
|
|
|
|
|
|
|
|
|
|
|
|
|
|
|
|
Barrel Finishing |
|
|
|
|
|
|
|
|
|
|
|
|
|
|
|
|
|
|
|
|
|
|
|
|
|
|
|
|
Honing |
|
|
|
|
|
|
|
|
|
|
|
|
|
|
|
|
|
|
|
|
|
|
|
|
|
|
|
|
Electro-polishing |
|
|
|
|
|
|
|
|
|
|
|
|
|
|
|
|
|
|
|
|
|
|
|
|
|
|
|
|
Electrolytic Grinding |
|
|
|
|
|
|
|
|
|
|
|
|
|
|
|
|
|
|
|
|
|
|
|
|
|
|
|
|
Polishing |
|
|
|
|
|
|
|
|
|
|
|
|
|
|
|
|
|
|
|
|
|
|
|
|
|
|
|
|
Lapping |
|
|
|
|
|
|
|
|
|
|
|
|
|
|
|
|
|
|
|
|
|
|
|
|
|
|
|
|
Super Finishing |
|
|
|
|
|
|
|
|
|
|
|
|
|
|
|
|
|
|
|
|
|
|
|
|
|
|
|
|
Forming |
|
|
|
|
|
|
|
|
|
|
|
|
|
|
|
|
|
|
|
|
|
|
|
|
|
|
|
|
Hot Rolling |
|
|
|
|
|
|
|
|
|
|
|
|
|
|
|
|
|
|
|
|
|
|
|
|
|
|
|
|
Forging |
|
|
|
|
|
|
|
|
|
|
|
|
|
|
|
|
|
|
|
|
|
|
|
|
|
|
|
|
Extruding |
|
|
|
|
|
|
|
|
|
|
|
|
|
|
|
|
|
|
|
|
|
|
|
|
|
|
|
|
Cold Rolling, Drawing |
|
|
|
|
|
|
|
|
|
|
|
|
|
|
|
|
|
|
|
|
|
|
|
|
|
|
|
|
Roller Burnishing |
|
|
|
|
|
|
|
|
|
|
|
|
|
|
|
|
|
|
|
|
|
|
|
|
|
|
|
|
Other |
|
|
|
|
|
|
|
|
|
|
|
|
|
|
|
|
|
|
|
|
|
|
|
|
|
|
|
|
Flame Cutting |
|
|
|
|
|
|
|
|
|
|
|
|
|
|
|
|
|
|
|
|
|
|
|
|
|
|
|
|
Chemical Milling |
|
|
|
|
|
|
|
|
|
|
|
|
|
|
|
|
|
|
|
|
|
|
|
|
|
|
|
|
Electron Beam Cutting |
|
|
|
|
|
|
|
|
|
|
|
|
|
|
|
|
|
|
|
|
|
|
|
|
|
|
|
|
Laser Cutting |
|
|
|
|
|
|
|
|
|
|
|
|
|
|
|
|
|
|
|
|
|
|
|
|
|
|
|
|
EDM |
|
|
|
|
|
|
|
|
|
|
|
|
|
|
|
|
|
|
|
|
|
|
|
|
|
|
|
|
Ra µm |
50 |
37.5 |
25 |
12.5 |
6.3 |
3.2 |
1.6 |
0.8 |
0.4 |
0.2 |
0.1 |
0.05 |
0.025 |
0.012 |
Ra µin (CLA) |
2,000 |
1,500 |
1,000 |
500 |
250 |
125 |
63 |
32 |
16 |
8 |
4 |
2 |
1 |
0.5 |
Useful Definitions
Term |
Definition |
Ra
AA
CLA |
Roughness average (Ra) is the arithmetic average of the absolute values of the roughness profile ordinates. Also known as Arithmetic Average (AA) and Center Line Average (CLA). The average roughness is the area between the roughness profile and its mean line, or the integral of the absolute value of the roughness profile height over the evaluation length |
Rq
RMS |
Root mean square roughness (Rq) aka Root Means Square (RMS) is the square root of the sum of the squares of the individual
heights and depths from the mean line.
|
Rp |
Roughness peak maximum profile peak height |
Rmax |
Maximum Roughness Depth is the largest single roughness depth w/in the elevation length. Rz expressed in micrometres or microinches. |
Rt |
Roughness total is the maximum peak to valley height. |
Rz |
Mean Roughness Depth (Rz) is the arithmetic mean value of the single roughness depths of consecutive sampling lengths. Z is the sum of the height of the highest peaks and the lowest valley depth within a sampling length.Rz = (Rp +Rp) |
Rzi |
Single Roughness Depth is the vertical distance between the highest peak and the deepest valley within a sampling length. |
Rv |
The maximum depth of the profile below the mean line. |
Sampling Length |
The reference for roughness evaluation. Its length is equal to the cutoff wavelength. |
1 µm |
"micron" a metric unit 0.001 mm or 0.0000394" |
0.1 in = tenth 0.01in = hundredth 0.001in = thousandth ("one thou") |
Need more information about our
Direct Metal Laser Sintering?
Please contact us at (561) 752-9095. Our highly skilled team of engineers and design technicians are ready to take on your most demanding Direct Metal Laser Sintering
projects from our prototyping services menu.